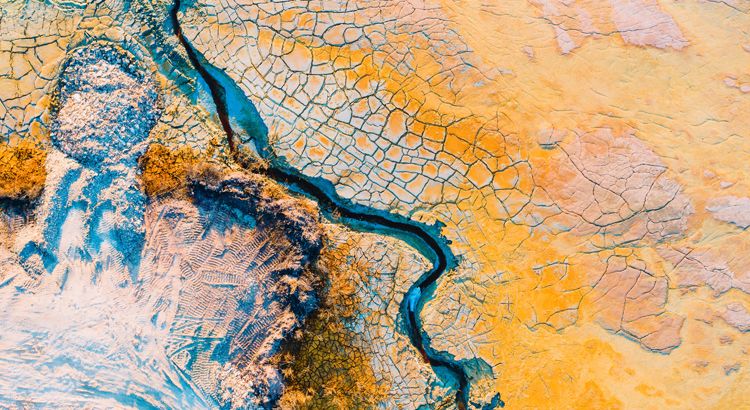
Durability begins with preparation
Shaun McQuaid
December 2, 2021
Welcome to fall! Just a few short hops from here to winter, and up here in the Northeast, we never know if the weather is going to be mild or wild. Either way, expect a lot of temperature fluctuations – the one constant here in New England is that the weather is never constant. With all the freezing and melting, it makes me worry about the long-term survival of my driveway – as the driveway freezes and thaws again and again, bad things tend to happen to its structural integrity, and it’s only a matter of time before I’ll have to take it down to the dirt and start over.
Fortunately, my driveway is both inert and unmoving. Imagine if it were bouncing up and down from 50,000 feet to ground level on a regular basis, and had active electronics embedded in it! The devastation would be extreme, my driveway not standing a chance.
Now think about the electronics that Mercury manufactures and assembles into OpenVPX and custom modules and subsystems. They are a lot more sensitive than my driveway and are subjected to a much more stressful environment. Going from desert tarmac to high altitudes causes a lot of thermal stress, particularly on circuit boards with large BGA soldered components - they tend to expand and contract noticeably due to shifting thermals. This is not solely a question of ruggedness – this is a question of durability and enabling products to survive for an extended life. And, as you might expect, this level of durability is not something that can be added after the fact – it needs to be designed-in from the beginning and manufactured with durability in mind.
Mercury’s MOTS (modified off-the-shelf) services provide exactly that level of durability and product life extension. Our OpenVPX products are designed from the start with the necessary leverage points to enable such durability enhancements as re-balling of solder, structural underfill, gold embrittlement mitigation and component staking. These processes can be tailored to include additional customer-specific requirements as well (we call this MOTS+). Due to the rigorous and repeatable testing that is part of our standard engineering practices, customers are able to reference qualification data that affirms our MOTS extended-life offering. This includes extended thermal cycling well beyond the standard rugged specifications. Mercury can offer the MOTS service affordably to our customers because our manufacturing operations in Phoenix, AZ, which can scale to support the largest electronics programs, includes all the necessary procedures and equipment to build MOTS modules to the most challenging specification.
Without MOTS, electronics can rapidly come to resemble my driveway – with cracks, gaps and lots of uncertainty about the future. But with Mercury’s MOTS processes, our customers can be confident they will get the long life from our electronics that they require.
For more details on Mercury’s MOTS offerings, please refer to our white paper.