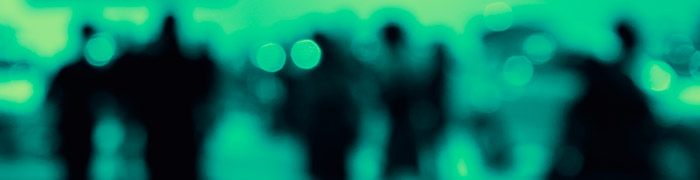
Enabling Edge Processing in Military Intelligent Sensors
Jennifer Keenan
March 14, 2019
In military environments, seconds can be the difference between life or death and mission success or failure. A soldier in hostile territory needs their mobile system to rapidly process sensor data to accurately analyze threats and take action. Intelligent sensor systems using artificial intelligence (AI) to make automatic critical decisions without human intervention rely on sophisticated algorithms to process sensor data real-time at the point of generation to ensure a rapid and accurate decision can be made. This real-time processing of data at the point of generation and consumption, decentralized from a data center or the cloud, is
Edge Processing. Each local system or device at the “edge” is self-sufficient to collect, process, store and disseminate data into action enabling the intelligent sensor and effector mission systems our military needs to carry out daily operations. These systems that enable mobile computing and artificial intelligence could be part of an unmanned aerial vehicle (UAV),unmanned ground vehicle (UGV) or a base camp collecting surveillance data of its surroundings to warn of incoming threats. Edge processing architectures require high speed, powerful processors, FPGAs specialized ASICs and many sensors supported by large amounts of high density memory and secure storage to accomplish their mission. A distributed network of devices and systems acquire various types of data from acoustic wave, biometric, optical, seismic and magnetic sensors. These connected platforms enabled by advanced application software, process this raw data and communicate meaningful insights real-time to the necessary local devices. The process data can then to sent to a centralized data center or the cloud for further use and storage.
Many of these systems or devices used for edge processing applications in forward deployed environments need to be small, rugged and agile relative to their data center counterparts. With limited space and high performance requirements, these architectures can benefit from custom microelectronics that combine processing, memory, sensors and other integrated circuits into a size, weight and power (SWaP)-optimized multichip module (MCM) or system in package (SiP). With expertise in system-level hardware and software architectures and ASIC devices, defense primes see little return on investment cultivating in-house capabilities to design and manufacture microelectronics using 3D packaging techniques. To simplify and optimize their design and development cycle, defense primes turn to trusted suppliers with expertise in advanced 2.5D and 3D packaging, high reliability manufacturing and specialized test capabilities.
Mercury Systems delivers a trusted and assured chain of custody from initial design through assembly and test for our defense customers requiring custom microelectronics to achieve best-in-class size, weight and power (SWaP) performance. Our world-class Phoenix, Arizona facility is Defense Microelectronics Activity (DMEA)-accredited for design, assembly and test for classified and ITAR solutions. Tightly integrated engineering, manufacturing and test resources enable production velocity, reduce security vulnerabilities and program risk. Our highly skilled and experienced employees coupled with our investments in state-of- the-art equipment and tools allow our customers to focus on creating next generation technologies to enable and protect our warfighters. Through the entire development cycle design, manufacturing to test, Mercury brings unique qualities to custom microelectronics solutions not offered by competitors.
- Design: Expertise in advanced miniaturization, 2.5D and 3D stacking and ruggedization technologies enable a custom microelectronic solutions in a size, weight and power (SWaP) optimized footprint.
- Thermal Management: Thermal design techniques channel heat dissipation from 160 to 800 W of power generated by today’s most advanced processors and FPGA devices through the use of multi-layer interlocked spreaders, customized thermal zones and the selection of ideal thermal composite materials to avoid overall CTE mismatch.
- Ruggedization: Recognizing that no two missions are identical, we design all of our solutions to meet mission-specific environmental performance requirements to gun-hardening levels.
- Simulation: Simulation and modeling of our complex designs enables rapid product development cycles and mitigates program risk. Mercury invests in world class tools to provide thorough performance data to drive successful custom designs.
- Manufacturing: World-class commercial manufacturing capabilities enable customers to jump to the front of the deployment race through rapid, low-risk, low-cost of ownership manufacturing. Our DMEA-trusted facility contains state-of-the-art equipment to realize the most complex custom solutions by mixing die attach, flip chip, wire bond and surface mount technology on the same device.
- Test: Mercury’s investment in comprehensive environmental test stations effectively test to MIL STD PRF-38534 (H and K) for hybrid microcircuits, STD PRF 38535 (M) for integrated circuits and MIL STD 883 for microelectronic devices. We specialize in developing custom test protocols to address application- and mission-specific reliability requirements.
To learn more about how Mercury can create a custom microelectronics solution to enhance your edge processing architecture with a SWaP-optimized device, visit custom microelectronics website or contact us at custom.microelectronics@mrcy.com.