-
APPLICATIONSARTIFICIAL INTELLIGENCEAVIONICS AND FLIGHT SAFETYC4ISRRADAR AND ELECTRONIC WARFARESECURE-PROCESSINGJOINT ALL-DOMAIN
-
DOMAINSLANDSEAAIRSPACECYBERSPACE
-
PRODUCTSAPPLICATION-READY SUBSYSTEMSMISSION-CRITICAL DISPLAYSRUGGED SERVERS AND SUBSYSTEMSRADAR TESTING AND TRAININGDATA STORAGE AND TRANSFERBOARDSMICROELECTRONIC COMPONENTSRF, MICROWAVE, MIXED SIGNAL
-
PARTNERSINTELNVIDIAXILINXMICRON
-
MERCURYCULTURECOVID-19THOUGHT LEADERSHIPSUPPLY CHAIN
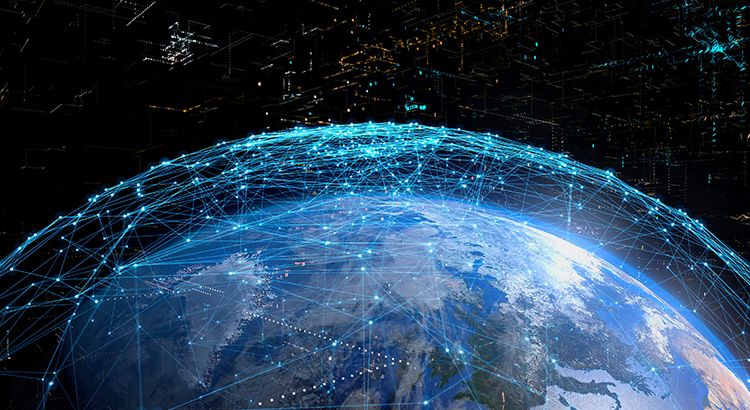
PEMs in space
Mario LaMarche
February 2, 2023
What are PEMs? PEMs, or plastic encapsulated microcircuits, are simply microelectronics encapsulated with plastic packaging. This straightforward process of taking a fragile silicon integrated circuit, surrounding it with plastic and making it sturdy enough to solder on a circuit board is common across many industries. The automotive industry alone uses millions of these devices. However, for some specific applications, there has been a reluctance to use this low-cost packaging approach. When a single device failure can take down a multi-million-dollar satellite, each design choice must be carefully considered. While PEMs work well in some industries, they are not necessarily as reliable as other options.
Space-Qualified Microelectronics
To understand the appeal of low-cost PEMs, it helps to know about the alternatives. Many high-reliability aerospace programs require all microcircuits be hermetically sealed in ceramic or metal packages. This packaging technology allows the microcircuits to be completely isolated from their environment—nothing, except the electrical signal, is getting in or out. As these packages are specially designed for harsh environments, they are capable of withstanding wide temperature ranges and mechanical forces.
As plastic encapsulated microcircuits are more closely examined, inherent attributes that lead to the possibility of a failure can be found. For example, unlike ceramic and metal, it’s possible for water vapor to penetrate the plastic, causing damage to the semiconductor devices. Thermal and mechanical stressors can potentially cause the plastic to crack. Additionally, as the PEM devices sit on a printed circuit board in a larger subsystem, they can emit trace amounts of gases in a process known as outgassing that can damage other parts of the system.
However, the automotive industry relies on PEMs—so why don’t we regularly see car crashes caused by microelectronic device failures?
Maximizing the Reliability of PEMs
While there are some inherent reliability challenges of plastic encapsulated microelectronics, the cost savings are significant. Not only is it a much less expensive manufacturing process, but the economies of scale allow for additional cost savings.
While some system architects mitigate the risk of device failure by adopting redundant design principles, there are also some steps device manufacturers can take to increase the reliability of their PEM products.
Device Upscreening
The concept behind upscreening is straightforward. Instead of using a custom-designed, space-grade component, why not take a commercial device and run it through extensive testing to ensure it will survive operation in harsh environments? Depending on the specific application, this testing can be extremely extensive and include electrical testing, environmental testing and radiation testing. Additionally, a sample qualification test is often performed that includes accelerated life testing and destructive physical analysis.
In order to standardize which tests are required, devices are often screened against published standards. For example, at Mercury Systems, one of the standards we screen against is NASA EEE-INST-002: Instructions for EEE Parts Selection, Screening, Qualification, and Derating. Digging down even further, our providers, such as Micron Technologies, ensure their DRAM components are rigorously tested and ready for extreme temperatures and performance demands.
Derating
In addition to confirming that the parts are capable of reliable operation in harsh environments, it’s critical to make sure there is significant margin in their operating conditions. For example, if the manufacturer’s specification is that the part can withstand up to 100 mA of current, the designer might derate that maximum to 80 mA—providing a margin to account for possible variation.
By lowering the electrical current through the device, the power dissipation is also reduced. Since the likelihood of failure is dependent on the internal device temperature, derating has the potential to increase the reliability.
A Trusted Supply Chain
An additional factor in maximizing device reliability is ensuring that it’s actually the device you think it is. Counterfeit semiconductor devices circulate through different industries and likely suffer from reduced performance and reliability. To prevent these parts from sneaking into a satellite, experienced electronic suppliers have multiple processes in place to ensure their supply chain is trusted. For Micron, this means direct memory probe points are eliminated and the memory packages don’t have exposed lead frames. Some of their memory products can indicate whether or not memory content has been altered. These processes typically limit the device suppliers to the manufacturer or approved distributors and require lot traceability.
Putting it all Together
Plastic encapsulated microcircuits might not be the best choice for every space program. Sometimes it makes sense to go with a custom hermetically sealed component. However, more and more programs are finding that PEMs are the right balance of price and reliability. This is particularly true in the New Space Economy where low-earth orbit (LEO) constellations are both more sensitive to price and expect shorter operational life than traditional space programs. Lastly, by using commercial technology, the latest advancements can be rapidly deployed to emerging applications—delivering new capabilities into orbit.